Tips for Selecting Industrial Ethernet Cable & Connectors
As industrial Ethernet is increasingly adopted, the purchasing of Ethernet network components often falls to electrical or installation contractors. If you are one of these people in charge of Ethernet cabling for an industrial application, you may think that you can save money by using commercial (office) cabling.
Unfortunately, the money you might save will disappear the first time there is a failure.
For example, a contractor installed a fire protection system for a large power generation plant, including the cabling. When it came time to run the network, it didn’t work.
Investigations revealed that the contractor had installed 4km (2.485 miles) of speaker wire instead of the industrial Ethernet twisted-pair cable specified by the engineers. Their reasoning: “It looked the same as the other wire”!
The outcome was that the contractor had to go back, pull the wire out, replace it . . . and pay for all of it. There goes the profit on that job. Today I am going give you 3 quick tips for selecting Ethernet cable and connectors for industrial applications—so you won’t make the mistake the fire protection system contractor did.
Industrial networks, such as those in a power generation plant require industrial cable and connectors to function properly.
Tip #1—Use Cable that Is Industrially Hardened
In the industrial environment you have to make sure the cable you use has the physical integrity necessary for the job. Harsh conditions are the norm; conditions such as shock, vibration, crushing and extreme temperatures routinely occur. Plus the cable may need to withstand intrusion from elements such as chemicals, water and debris.
“Industrial hardening” is a term that describes a cable’s (or other product’s) ability to withstand conditions that aren’t typical in a commercial environment. Within the range of industrially hardened products, there are a wide variety of specifications that can be mixed and matched.
In addition, regulations exist to define the tolerances that the cable must meet for a variety of applications where reliability or safety is an issue.
The regulations vary by industry and by geography, thus you want to make sure you have the right cable for the particular project. The cable characteristics you choose for an oil and gas application in Texas are not necessarily the same as those for a power substation or a machine shop in Canada.
Tip #2—Use Cable with Good Electrical Performance
In a manufacturing facility there can be a lot of “electrical noise” generated by the equipment. This noise is caused by random fluctuations in electrical signals and it can impact the integrity of signals being transmitted over cable.
Ethernet twisted-pair cabling, which is an industrial staple, is often installed where it is subject to rotation, stretching and bending. This can result in irregular gaps between the conductors in the cable and these gaps can degrade signal integrity.
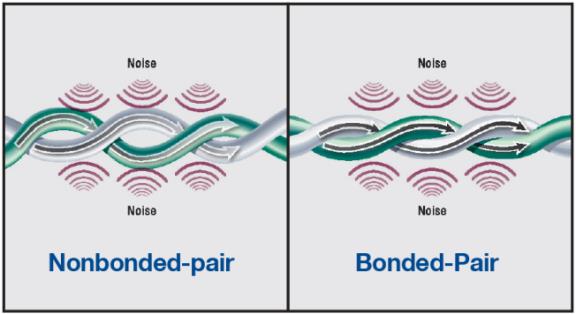
To avoid that, use cables manufactured using our unique “Bonded-Pair” technology. With this cable, the twisted pairs are bonded along their longitudinal axis to guarantee uniform spacing. This bonding gives the cables greater immunity to signal degradation from bending, twisting and electrical noise.
Cable that is bent or twisted can develop gaps between pairs, which can lead to signal degradation. Belden’s Bonded-Pair technology prevents gaps from forming, delivering consistent electrical performance including greater immunity to noise.
In high-electrical-noise environment, you may also need to consider shielded cable, which protects against both electromagnetic interference (EMI) and radio-frequency interference (RFI).
Tip #3—Use the Right Connector for the Environment
Don’t choose the right cable but the wrong connectors. If the project is in a harsh environment, you may need special connectors as well as special cables.
If the environment is one where corrosives or dust may intrude and damage conductors, then sealed connectors are most suitable.
If vibration is an issue, then screw-type connectors that stay fastened when shaken are highly recommended.
Another alternative is factory-assembled, factory-tested cord sets (the cable plus the connectors at either end) which provide high reliability and reduce installation time.
Select the Right Cable for Your Application
The bottom line for selecting the right cable is to make sure it is sufficiently hardened, has high electrical performance and is shielded to protect against electrical noise. Commercial cable will not work in most cases.
If the cable has the right certifications for the application in question, then it will likely do the job.
You can do the legwork yourself to check this. However, in the end, it might be easiest to purchase and install the cable specified by the network design engineers.
Don’t be the contractor that has to pull out and re-install 4km of cable!